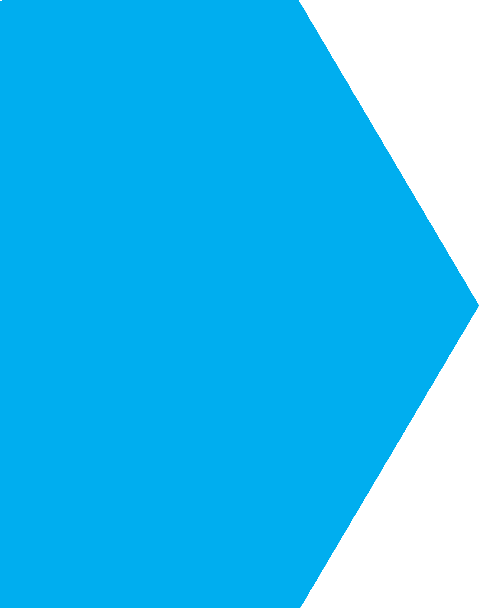
Unleash the power of your Textile Rotary Printing Machine by using Gurjar NEO+ Series: A New Era in Super Fine Textile Rotary Printing Starts Here!
GURJAR Screens introduces to its Fourth Generation family of screens compromising of NEO+ Series 210 Mesh, a new NEO+ 225 Mesh Screen type to the international rotary textile-printing world. NEO+ 225 Mesh Screen is the result of more than 5 decades of experience and innovation in rotary screen-printing solutions and features the top end of Gurjar Screens collection. This screen is an addition to established NEO+ brand of Third Generation Screen, which deliver the best printability and high-end printing definitions.
The new NEO+ 225 Mesh Screen combines the benefits of the existing NEO+ 135ED, 165ED, 195ED and 210 Mesh screens thus breaking the mesh barrier again in the world of textile rotary screen-printing technology. This is once again a FIRST in screen making across the world and it aids to challenge very high-definition designs.
The characteristics of this series lies in its ability to tackle designs required at very higher resolutions – from finest lines (saw tooth effects virtually eliminated especially for horizontal lines) and half tones (moire patterns eliminated) to multi colour creations combining different design types.
The new screen has a number of benefits:
1. The highest ever printing resolution in textile rotary printing
2. Improved surface printing due to very high fine detail definition
3. Benefits in half-tone and geometrical printing with even more effective biconical hole shape
4. Can challenge the most challenging design creation in rotary printing
REPEAT | MESH | PKG |
---|---|---|
640 | NEO+ 210 | 10 |
640 | NEO+ 225 | 10 |
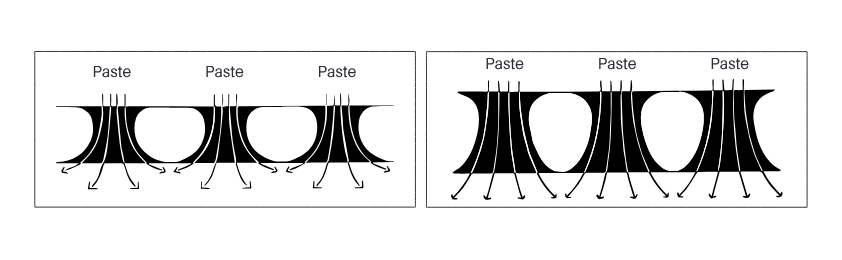
Screen Parameters
To fully understand the benefits of the NEO+ range of screens, one must appreciate the general screen characteristics – The open area, mesh count and screen thickness – they all have a close relation.
This is due to the nickel growth occurring during the screen manufacturing process. Simply put, a higher mesh count and a higher thickness of the screen decreases the open area. During the screen making process, the nickel grows from the mandrel in both directions, to the top and to the sides.
Using the expertise in electroforming chemistry gathered over more than 50 years, GURJAR Screens is able to steer the nickel growth mainly in the top direction. This way, the dam shape stays thin and gets streamlined. Therefore the ratio between the hole-size, mesh count and thickness of the screen can be pushed beyond the conventional boundaries of the rotary screen-printing industry
With the dam width decreasing and higher open area improves the screen’s printability exponentially. Less printing pressure is needed to achieve a decent coverage of the substrate. Therefore the new NEO+ range of mesh screens can even save paste consumption and are more cost effective in comparison to other generation mesh screens. These screens are best suited for full penetrative printing as well as surface printing, both providing the best possible printing resolution in textile printing.